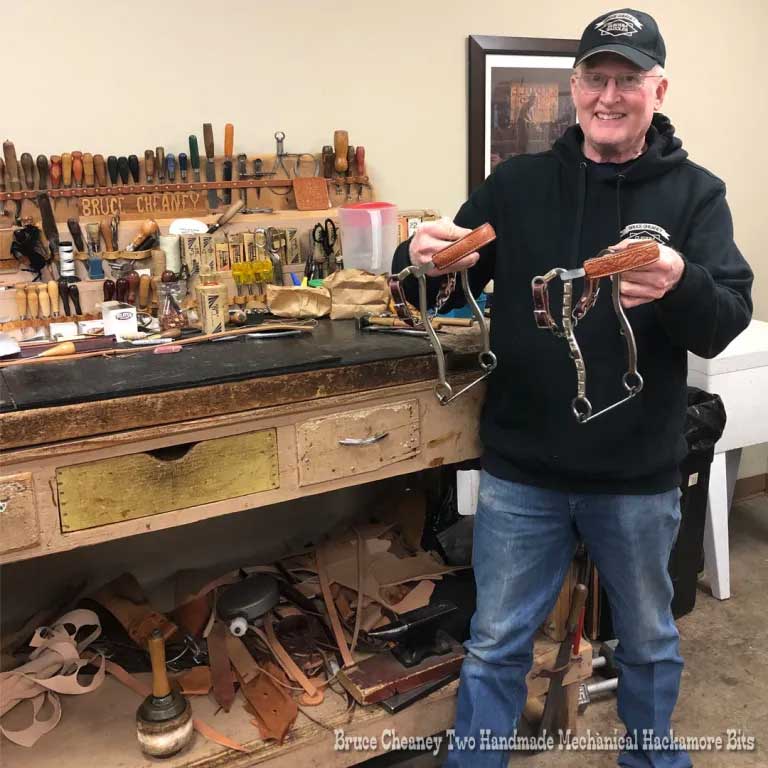
Let’s jump back in time about 150 years. A great fire has turned Chicago into a city of ashes. The James Gang had robbed its first train robbery. Cowboys are driving thousands of cattle up from Texas to the railheads in Kansas. And Charles D. Cheaney has opened up his saddle shop in Gainesville, Texas.
Five generations later, Bruce Cheaney, 71, is making saddles with the same attention to detail that his leather stitching ancestors did. Today, Bruce Cheaney is doing much more than making great saddles and leather work. He is introducing new generations of craftsmen to the wonders of leather work. Don’t believe me? Try tuning into https://www.youtube.com/cheaneysaddles, Bruce Cheaney’s YouTube channel, which has more than seventy-eight thousand followers. Even if you know nothing about the craft, Bruce will inspire you to pick up a piece of leather and start to work.
Why is his channel so popular?
“Leather working is a good way to express yourself through your work,” Bruce says with typical humility. It’s more than the appeal of leather work that makes Bruce Cheaney’s online and real-time work so popular. It’s the grace of his manner, his soft North Texas accent, and the obvious skill that he brings to his craft.
“Hello. Bruce Cheaney here in the saddle shop in Gainesville, Texas,” Bruce says to introduce one of his YouTube tutorials in his soft North Texas drawl. Bruce is all work but has the easy manner of your neighbor. He’s not Mr. Rogers. He’s not Roy Rogers. He’s the real deal.
“My most popular products are custom-made saddles and handmade mechanical hackamore bits with a flat leather nose band.” Yup, Bruce is best known for his saddles and tack, just like the Cheaney’s that have worked in Gainesville for a century and a half.
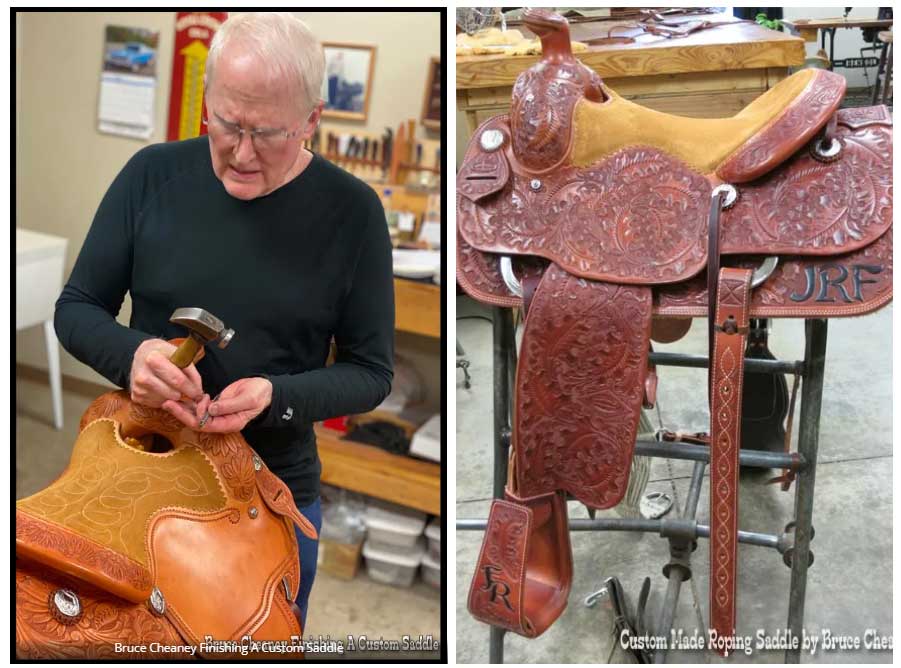
The tradition of saddle making goes way, way back, about 6,000 years back, to the time when horses were first domesticated. People have made saddles for camels, oxen, and even an ostrich or two, but making saddles for horses has always been the core of the saddle making business.
Eurasian nomads, Alexander the Great, Chinese Emperors, Roman Legionaries, the knights of the Middle Ages all used saddles, not just as tools to improve their horsemanship but also as symbols of power and taste. The modern western style saddle with a solid saddle tree, pommel, and stirrups has been around for hundreds of years. The western style saddle was first introduced into what is now the United States by Spanish conquistadors, who raised cattle and fought bulls on what we would recognize as western saddles.
A saddle is not as simple as it may appear. Saddles come in a wide variety of styles each designed for a specific equestrian discipline. The most important thing about a saddle is that it must be comfortable for both rider and horse. Making that happen is a challenge. A rule of thumb is that the saddle must not do any damage to the horse’s withers, and it must give a rider the proper balance to perform on horseback, whether he or she is roping, cutting, or trail riding.
“I use only the best saddle trees made by maker’s who know how to make a saddle tree that fits,” Bruce says. “I also have specs for saddle trees that have worked for me for many years.”
Bruce makes his saddles by hand featuring vegetable-tanned leather hand-carved and tooled in oak leaf and acorn pattern. He builds a saddle seat with loop-through stirrup leathers, and he makes the fenders, or pieces of leather on the side, with roughout leather to enhance the rider’s grip.
“Custom roping saddles are my favorite saddles to make,” Bruce says.
“I love to make heavy duty roping saddles that perform well and are comfortable for both horse and rider.”
Bruce is also well known for his mechanical hackamores. Decades ago, cutting horse champion Matlock Rose from Gainesville asked Bruce to make him a hackamore bit with long leverage so he wouldn’t have to hurt his horse’s mouth. Matlock Rose liked the tack so much, he became a regular visitor at the Cheaney’s shop.
Building a hackamore requires working with metal, a skill that Bruce has mastered in addition to his leather work. According to Bruce, “Metal working requires a separate workshop because of the grinding dust and equipment such as a Tig welder and heavy-duty belt sanders.”
Bruce’s customers include ranchers, working cowboys and well-known horsemen including J.D Yates, Frank G. Merrill, and the late Sam Rose and Robbie Schroeder.
Many of Bruce’s clients have become life-long customers. How has Bruce managed to develop such a loyal clientele? According to Bruce, “They just like what I make.”
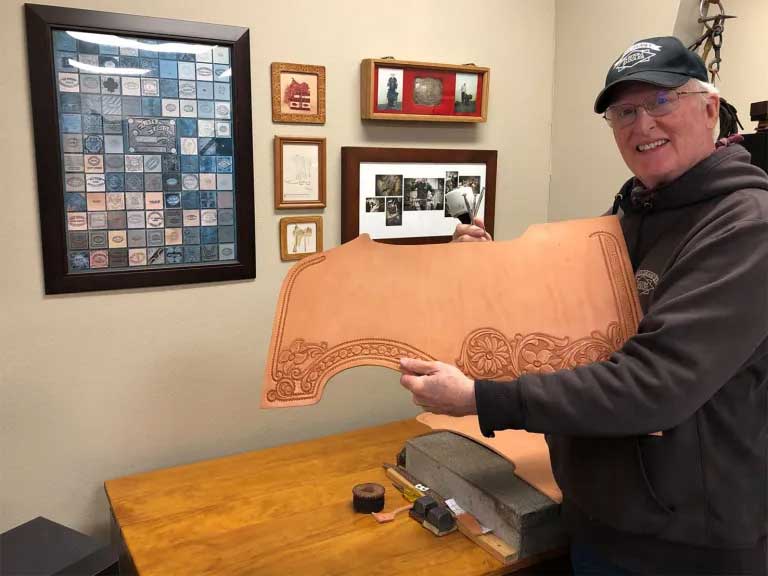
Bruce also enjoys making belts, sheaths for knives, and even coasters. “The most challenging project I have ever worked on was a longhorn skull mount that I tooled and carved and antiqued. I also had to make the mounting brackets for it.”
No matter what his clients want, Bruce is up to the challenge. “A friend of mine asked me to make him a pair of hunting knives and sheaths. I made the handle with deer stag from the Stark Ranch. I added a concho bead on the end of the handle with the ranch brand. It took me two weeks.” Craftmanship takes time, but his clients appreciate Bruce’s attention to detail which is part of the Cheaney heritage.
“Joseph Madison Cheaney, 1808 – 1863, was listed in an 1850 census as a Baptist preacher and saddle maker,” Bruce says. “My Great Grandfather Charles D. Cheaney moved to Gainesville, Texas in 1877 and set up a saddlery and harness shop,” At that time, Gainesville, which is only seven miles from the Oklahoma border, was a supply point for cowboys driving cattle herds.
“My grandfather Sterling Price Cheaney worked in that shop too. Then later the shop ran under the name Cheaney & Woods. W.L. Woods was Charles D. Cheaney’s son-in-law.”
When the cattle boom faded, Gainesville thrived as an agricultural center. Nearby oil discoveries gave the town an added economic boost. Through it all, the Cheaney family kept on making saddles. “After the passing of W.L. Woods my grandfather Price Cheaney bought the shop from Wood’s widow and moved it to the corner of Main and Dixon in downtown Gainesville. Price and Blanche Cheaney had four son’s Harold, Charles, Thomas and Jack Cheaney, my father. This shop ran until the mid-1950’s.”
Bruce began building saddles as a boy, learning how to cut and craft every part of a saddle, from the cinch to the latigo. “I learned leather working and saddle making from my dad as well as my two brothers Pat and Phillip Cheaney,” Bruce says. Bruce and his wife Karen opened up their own saddle shop in Gainesville in May of 1981, just two years after they were married.
Phillip and his daughter Nicole own Cheaney Tack just down the street from Bruce’s shop. “Phillip can be pretty competitive.” Bruce laughs. “If he finds something new, he will make a couple hundred of them before he tells me anything.”
Today, Gainesville, Texas is a city of 17,000, the seat of Cooke County, and a tourist and manufacturing center for Texoma, as the area along the Texas-Oklahoma border is known. As Gainesville has changed over the decades, so has Bruce’s business. The craft of saddle-making hasn’t changed, but marketing sure has.
How did a traditionalist like Bruce Cheaney become a saddle-making YouTube star?
“My son Tom picked up a Sony mini camera one day here in the shop and said to me, ‘Here do something.’ I was fitting a saddle seat in a saddle, and we filmed the process. Then Tom set up the @cheaneysaddles YouTube Channel. It just kind of happened. I really did not know what I was getting into,” Bruce chuckles.
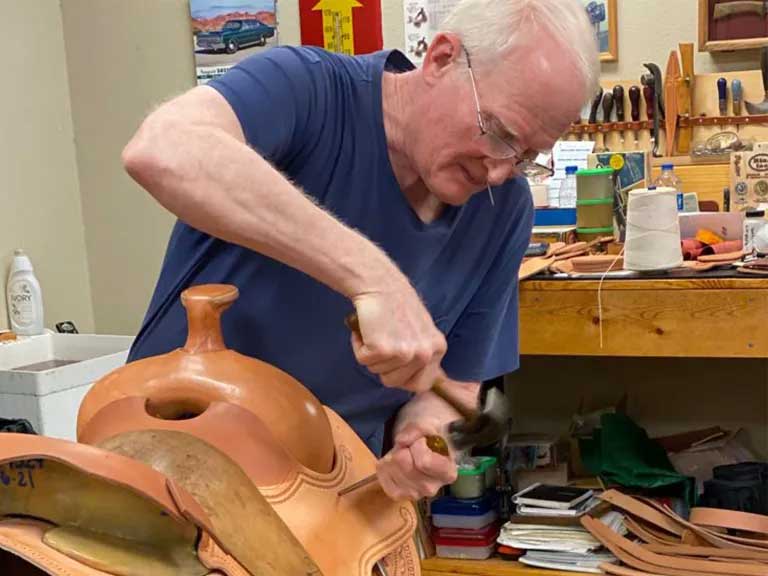
One of the first series Bruce posted documented a saddle restoration project in which Bruce repaired and cleaned up a leather saddle that was made by his family in 1946. “This saddle repair project took two months to complete,” Bruce explains on his YouTube channel. “A lot of the components had to be replaced in order to bring the saddles back to a usable condition. New stirrups, saddle fenders, flank straps, cinches and catchers. The saddle oil I used really helped recondition the leather bring it back to life. These custom-made roping saddles have seen a lot of use in the arena and were just about used up and consider un-repairable, but I took them in and did my thing to them.”
Bruce’s “thing” was good enough to bring the beat-up saddle back to its former elegance and the series has stood the test of time. It is as fascinating to watch as it was when it was first posted more than ten years ago.
Bruce has followed up the restoration video with a series of other how-to YouTube tutorials including: The Art of Hand Sewing Leather, How to Draw Leather Tooling Designs, Leather Carving for Beginners and Leather Burning, Pyrography and Steps in Making Spurs.
In his tutorials Bruce explains the basics of his craft and how to use a variety of tools including, awls, needles, threads punches and trimming knives. “I have a lot of tooling and carving leather videos. It gives newcomers to leathercraft and leather working confidence to give it a try.”
Most of these series have five episodes, with a total running length of less than an hour. Judging from viewer response, Bruce has really hit the YouTube sweet spot.
“I still watch all your videos, Bruce! You are inspiring! Thank you for all you have done for the art.”
“This is so incredible! So, satisfying to watch a master at work 🙂 Great job Bruce!”
“One of my childhood memories is lying in bed waking up, it might be two or three in the morning to the sound of my dad tapping on leather. He was also a great leather carver. Your work has to be the closest I have seen to his, extremely sharp and clean.”
“Love your videos… Enjoying here from Brazil…”
Whether they are from Brazil or Gainesville, Bruce appreciates his YouTube fans. He offers everyone who wants to take up leatherworking a piece of advice. “Keep it simple and just get enough high-quality tools to get started then add to your collection of tools after you figure out what you need.”
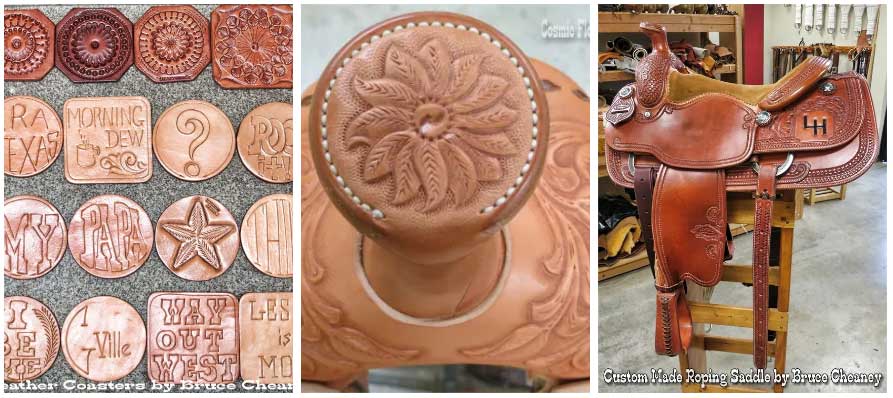
Bruce’s YouTube fans get a good look at his workshop in Gainesville. “My saddle shop is just about the right size for one or two workers. There’s plenty of room to get around and be energy efficient. Leather racks and work benches, a stamping bench, and a pattern cabinet line the walls. I have three sewing machines a Cowboy CB-4500 and a Singer 3115 plus an old Singer patching machine. My favorite tool is a small, curved blade knife much like the old Hyde leather knives,” Bruce says.
“Tooling and carving leather are the most enjoyable aspects of my work. I just love to carve leather. Sometimes I just sit down and carve some leather coasters for fun and practice. Some turn into artwork and some don’t.”
An artisan steeped in the traditions of his craft; Bruce has a bit of a wild streak. “One of my dream projects is to make some cigar box guitars,” he says. Any pickers out there interested?
When he is not in his studio, Bruce enjoys spending time with Karen, his wife, his three children, Thomas, Carey and Candace, and his church family.
His daughter Carey is putting her own spin on the family leather trade producing a distinctive line of handmade leather bags, clutches and jewelry. Bruce proudly notes that his son Tom has made twenty-two saddles.
“I have seven grandchildren,” Bruce says with pride, “and they are all creative and artistic.”
“My grandson Sage is all over horses. He’s a bronc rider. I just finished giving him some leather working training sessions on Saturday afternoons. He seems interested so I got him a set of tools for his 16th birthday. Sage is going to be the seventh generation of the Cheaney family to work leather. He’s really a country boy.”
Bruce is gratified to see Sage and his other grandchildren taking an interest in his work, but he has no interest in setting aside his tools. “I plan to keep on making one of a kind, handmade items,” Bruce says. “I have no plans to stop until I can’t do it anymore.”
These are the words of a truly legendary saddle maker, Bruce Cheaney.
This article originally appeared on Shoptalk Magazine and is published here with permission.
You can find all kinds of interesting articles in our section on Tack & Farm.